При облучении поверхности тела светом энергия квантов (порций) света поглощается этой поверхностью. Образуется теплота, температура поверхности повышается. Если световую энергию сконцентрировать на малом участке поверхности, можно получить высокую температуру. На этом основана сварка световым лучом оптического квантового генератора — лазера. Лазерный луч легко управляется и регулируется, с помощью зеркальных оптических систем легко транспортируется и направляется в труднодоступные для других способов места. В отличие от электронного луча и электрической дуги на него не влияют магнитные поля, что обеспечивает стабильное формирование шва. Из-за высокой концентрации энергии (в пятне диаметром 0,1 мм и менее) в процессе лазерной сварки объем сварочной ванны небольшой, мала ширина зоны термического влияния.
Применение импульсного лазерного излучения с длительностью импульса в несколько миллисекунд дает возможность получать зоны термического влияния на материал детали не более сотых долей миллиметра. За счет очень малой зоны термического влияния основной материал детали практически не нагревается (справедливо для толщин > 1мм), скорость охлаждения расплава на поверхности 102…103 °С/сек. При этом формируемый слой материала получает мелкодисперсную структуру с высокой износостойкостью, отсутствует коробление и поводки детали. Микроминиатюрный инструмент (луч лазера) вкупе с тонкими присадочными электродами позволяет свести последующую механическую обработку к минимуму — припуски под последующую механическую обработку 0,1…0,3 мм. Слой присадочного материала имеет хорошую адгезию с основным материалом (> 300 МПа). Присадочный материал перемешивается с основным только в зоне контакта, поэтому физико-механические характеристики наплавленного слоя определяются по большей части составом присадочного электрода, параметрами лазерного импульса (длительность, мощность, форма).
В основном процесс ремонта наплавкой выполняется вручную с визуальным контролем через микроскоп с защитным затвором или монитор, подключенный к видеокамере, которая расположена в оптической системе оборудования. Чаще всего используется для восстановления повреждённых деталей машин и дорогостоящей оснастки. Роботы наплавляющие присадочной проволокой распространения пока не получили в силу двух основных причин: уникальности дефектов которые нужно исправлять и, соответственно, потребности в огромной работе программиста, требуемой для управления роботом на сложной, не типовой поверхности дефекта. Вторая причина — сложность контроля натяжения присадочной проволоки и ориентации ее подачи.
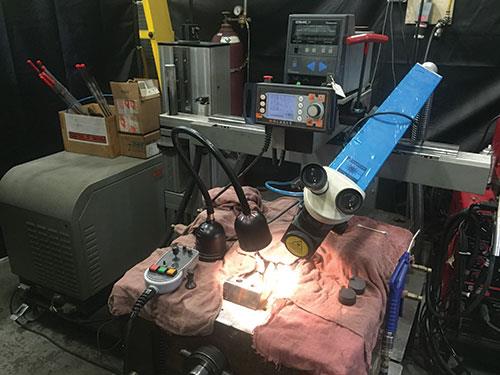
Основными параметрами, определяющими качество наплавленного слоя, кроме химического состава присадочного материала, являются длительность, мощность , форма лазерного импульса а также положение точки фокуса луча, наличие или отсутствие защитной среды. Все эти параметры влияют на процессы нагрева, расплавления и кристаллизации свариваемых материалов (так как процесс наплавки есть, по сути, процесс сварки с присадочным материалом). Современные системы управления накачкой лазера позволяют регулировать длительность импульса, а также распределение энергии в импульсе. Возможно задание в качестве рабочей прямоугольной формы импульса — она является наиболее энергоемкой и обеспечивает передачу наибольшего количества энергии обрабатываемому материалу. Во многих случаях именно такая форма и применяется. Однако, в некоторых задачах такая форма не оптимальна. Время фронта и спада импульса определяют скорость плавления и кристаллизации материала в сварочной ванне. Это влияет на образование пор в создаваемом шве, склонность к горячим и холодным трещинам. Так, для сварки высокоуглеродистых сталей, чугуна, литейных алюминиевых сплавов, склонных к образованию горячих и холодных трещин, используется форма импульса с сильно увеличенным временем заднего фронта. Для материалов с гальваническим покрытием, отливок с высокой пористостью, низкоплотных материалов порошковой металлургии оптимально применение импульса с увеличенным временем переднего фронта. Импульсы с коротким, мощным передним фронтом и уменьшенной энергией в основной длительности используются при работе с металлами, имеющими высокий коэффициент отражения излучения и проводимость (чистая медь, серебро, отдельные алюминиевые сплавы).